PRISM CCD testing data
reduction package user manual
Contents
1 . Linearity (classical way of doing)
2. Charge transfer efficiency (CTE)
3. Quantum Efficiency
4. Readout noise
5. Dark current
6. Linearity (using TDI images)
7. Conversion factor using 2 bias and 2 flats
8. Charge transfer efficiency using Iron 55 source

Menus of the CCD test data reduction package
This user manual is intended to explain how the images have to be acquired and
processed with the PRISM's CCD testing package.
The parameters determining the CCD performances
(such as linearity, dark current, conversion factor ...) will not be explained
in this page. The user should have the basic knowledge about CCDs. Many books
about this subject has been written (see references section).
Those procedures are used at ESO in order
to characterize CCD cameras before being installed to the telescope or for CCD
preliminary testing.
For a given test, requiring many images, they ALL must have the same amount
of pixels (i.e. width/height) and being the same data file type (i.e.: integer
or floating point data). Mixtures of image seize and/or data type will result
directly in a failure.
1. Non-Linearity and Conversion Factor (e-/ADU)
This measurement is used to get the conversion factor (e-/ADUs) and the CCD
linearity.
The CCD must be illuminated by a very stable light source, the resulting image
has to be as "flat" as possible.
10 couples of images, at least, must be acquired with different exposure
times, ranging from the full dynamic (intrinsic CCD dynamic or Analog to Converter
dynamic) to the bias level.
For instance : (16 bit camera ranging from 0 to 65535 ADU)
PRISM file image (CPA of FITS file type)
|
Exposure time (Sec)
|
Mean (ADU)
|
image1.cpa
|
10
|
12152
|
image2.cpa
|
10
|
12155
|
image3.cpa
|
2
|
2178
|
image4.cpa
|
2
|
2185
|
image5.cpa
|
50
|
62535
|
image6.cpa
|
50
|
62534
|
......
|
........
|
.......
|
Take at least 16 couples of images and try to achieve up to 95% of saturation
level, to explore the all range.
Avoid to take images with increasing or decreasing exposure times as for
instance 2,5,10,50 sec, use instead a random order as 2,50,10,5 sec.
When the PRISM software dialog box pops up, you have to enter a window where
the stats will be achieved (X1,X2,Y1,Y2). Keep in mind not to include defects
in this window. The statistic can be either "median" or "classic" type. Set
the "median" to avoid the effect of out of range or defective pixels, median
is less sensitive to local contaminants.
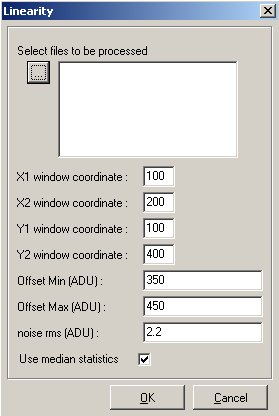
The range (offset min et max.), comes from the offset image mean. In that
case supply : Offset/bias level min = Offset -10% and Offset max= offset
+10%), this allows to optimize the offset deviation effect with respect to shutter
errors. To known this figure (Bias level), you have to measure it form a set
of bias images.
!! Multiples files can be selected by keeping the ALT
key down while selecting files in the open dialog box !!
PRISM software compute automatically the conversion gain in e-/ADU
and the residual non-linearity expressed in % units, using the whole double
exposure set of images. A photon-transfer curve is plotted as an output.
Results
Console output :
Optimum offset(ADU) (1): 368
Non linearity (Peak to peak) : (1): 0.4367% / -0.8695%
Optimum offset(ADU) (2): 368
Non linearity (Peak to peak) : (2): 0.3741% / -0.1807%
Conversion factor e-/ADU : 1.9926
-> RMS error : 0.12428
Readout noise (e-) : 4.7822
The data(1) uses the first set of images and data(2) the second set.
The following curves are displayed, no need to make a table sheet for
a plotter like Excel.
Linearity curve according to exposure time.
Residual non linearity curve
Photon transfer curve, this plot is used to compute the
conversion factor (e-/ADU).
VERY IMPORTANT : be aware that FITS
files are coded sometime as a true 16 bit data (0-65535). PRISM adapts data
type according to the input file and to save memory space, but we recommend
strongly to open the "Option/FITS options" menu, and to set the "Load
16bits unsigned FITS file to floating point data" as checked.
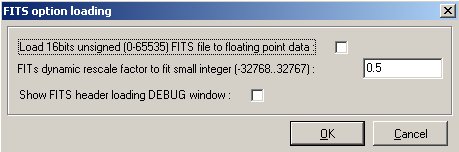
2. Charge transfer Efficiency (CTE) EPER method
This is the dialog box related to CTE measurement :
For this purpose, acquire a single flat field image reaching 95% of
the ADC dynamic range. The camera shall be able to read the array beyond the
photosensitive area. This area beyond the image is called "OVERSCAN", and contains
fake pixels having the bias value provided by the electronic readout chain and
CCD. This area shall be extended both in X and Y directions. This kind of image
has to be provided to PRISM software to compute CTE.
Y1,Y2 is the area to perform the mean of the last light sensitive row and
the X1,X2 is the range to compute the last mean column. The number of transfer
across X and Y is typically the light sensitive image part.
Console output:
Loading :F:\Images\Frankie\CTE\Cte_0001
Mean -> Last X :58491.6583936574 Last X+1 :469.123061013444 Overscan area
:449.922095829024
Horizontal CTE = 0.999999838470179 / 6 nines
Mean -> Last Y :65510.6978248089 Last Y+1 :495.093474426808 Overscan area
:445.12810646144
Vertical CTE = 0.999999625037444 / 6 nines
Method used :
The method employed here is the EPER (Extended Pixel Edge Response). This method
is not really accurate and the IRON 55 tests are much more reliable. Some CTE
figures greater than one can be measured with this method !
3. Quantum efficiency and PRNU (Photo Response Non
uniformity)
This is a really difficult measurement, because the result has to be provided
in absolute figures, and you MUST have to input calibration data.
Basic knowledge regarding QE measurement must be known
!!
The usual scheme is to use an absolute quantum efficiency calibrated photodiode
installed at the same position as the CCD will be, and to use flat field images
made in the front of an integrating sphere, fed by one or two monochromators.
This setting allows you to get different flat field images at different wavelengths
and short bandwidth.
The incoming light wavelength is typically ranging from 300 to 1100 nm, with
a short bandwidth, such as 5nm. The photodiode current is measured, and the
photodiode manufacturer calibration curve enables you to compute the amount
of photons per square centimeter and per second. This is an example of a photodiode
calibration file (as a text file) :
# No TABS
# ratio bdw 4 # col 1 Wavelength
# col 2 Flux on the CCD surface, expressed in photons/sec/cm2
# col 3 Current that is measured at integrating sphere level or closeby
to the CCD
320 1.1e+8 0.209e-9
340 2.55e+8 0.544e-9
360 5.18e+8 1.115e-9
380 9.27e+8 2.124e-9
400 1.44e+9 3.646e-9
450 2.9e+9 7.94e-9
500 3.54e+9 10.207e-9
550 3.9e+9 11.5e-9
600 3.97e+9 11.74e-9
650 3.6e+9 10.85e-9
700 3.09e+9 8.96e-9
750 2.35e+9 6.67e-9
800 1.54e+9 4.224e-9
850 1.66e+9 4.52e-9
900 1.42e+9 3.871e-9
950 3.4e+9 8.6e-9
1000 3.16e+9 7.65e-9
1100 2.42e+9 1.224e-9 Afterward, the optical
transmission of the dewar window according to the wavelength as to be provided
(as a text file).# Window transmission
# col 1 Wavelength
# col 2 Relative transmission
320 0.94
340 0.97
360 0.98
380 0.98
400 0.99
450 0.99
500 0.99
550 0.996
600 0.9856
650 0.9615
700 0.926
750 0.889
800 0.8517
850 0.8153
900 0.7873
950 0.7627
1000 0.7466
1100 0.723
IMPORTANT : For all the wavelengths used, calibration
photodiode text file and window calibration transmission text file MUST match
each other. It means that the same wavelengths must be entered in the two calibration
files (Otherwise an error will occur). FITS files must include the following
HEADER Keywords :
WAVLG = 550 // Central
wavelength : Expressed in mn
BANDW = 5 // Bandwith : Expressed in mn
FLUX = 1.2E-5 // Photodiode current expressed in Amps
or
1_FLUX = 1.2E-5 // Photodiode current expressed in Amps
Regarding the CPA image file : if images have been acquired with PRISM, the
previous figures are entered automatically into the CPA file header.
A reference offset/Bias image (resulting from a median stack of 10 offset/bias
images) is mandatory, also the integration time must be limited in a way that
the CCD dark current remains negligible.
Once having entered all the calibration files in the software dialog box,
the analysis window X1,X2,Y1,Y2 must be chosen in the way that it must
not have any serious defects (black hole, bright pixels).

Conversion factor must have been measured previously (see method 1 or 2).
Distance during calibration/measurements allows the reference photodiode not
to be at the same distance as the CCD, and to apply a 1/d^2 correction. This
correct for few centimeters effects.
Results
This is the console output results, for each FITS files, it yields to
:
Wavelength in nm ; Flux in
Amps ; Exposure in sec ; Count values in e-
Filename Wavelength
Flux Exposure Mean
Stddev.Rms Median Mean-Median
QE0002.fits 320
1.749E-10 180 21400 484.08
21400 -0.051972
QE0034.fits 340
4.754E-10 180 60662 1281.8
60678 -15.768
QE0004.fits 360
1.0234E-9 79.523 60965 1260.3
60976 -11.264
QE0032.fits 380
2.0072E-9 36.67 60579 832.35
60568 10.537
Qe0006.fits 400
3.5871E-9 20.472 60341 578.48
60342 -1.3613
QE0030.fits 450
8.4612E-9 9.223 60576 473.26
60582 -6.0853
QE0008.fits 500
1.1307E-8 7.248 60050 462.21
60052 -2.3795
QE0028.fits 550
1.3328E-8 6.904 64220 478.24
64226 -5.6408
QE0010.fits 600
1.4012E-8 6.438 59948 446.82
59952 -4.0484
QE0026.fits 650
1.3279E-8 7.296 59910 442.79
59914 -4.2144
QE0012.fits 700
1.1196E-8 9.48 59680 450.23
59686 -5.5382
QE0024.fits 750
8.4697E-9 14.39 59830 481.27
59838 -8.0172
QE0014.fits 800
5.4537E-9 27.831 59990 533.66
60004 -13.601
QE0022.fits 850
5.9775E-9 33.177 59951 508.76
59960 -9.061
QE0016.fits 900
5.1913E-9 58.056 59327 941.36
59162 165.3
Qe0020.fits 950
1.2662E-8 49.111 61606 2471.5
62156 -549.94
QE0018.fits 1000
1.0568E-8 171.99 62739 3667.6
64178 -1438.6
QE0036.fits 1100
1.7114E-9 180 1006
82.472 994 12.022
Image #1 Bandwidth :5
PhotoDiode calibration Bandwidth :4
Filename Wav. PRNU%
QE% FDio/FDio.cal Ph/pix/sec
e-/pix/sec %Wind
QE0002.fits 320 2.262
61.065 0.83684
207.12 118.89 94
QE0034.fits 340 2.1125
69.312 0.87389
501.4 337.1
97
QE0004.fits 360 2.0669
73.139 0.91787
1069.8 766.77 98
QE0032.fits 380 1.3742
85.51 0.94499
1971 1651.7
98
Qe0006.fits 400 0.95867
93.401 0.98385
3187.7 2947.5 99
QE0030.fits 450 0.7812
95.421 1.0656
6953.3 6568.6 99
QE0008.fits 500 0.76969
94.847 1.1078
8823.7 8285.3 99
QE0028.fits 550 0.74462
91.842 1.1589
10170 9302.7 99.6
QE0010.fits 600 0.7453
88.622 1.1935
10661 9312.2 98.56
QE0026.fits 650 0.73904
86.151 1.2239
9913.7 8211.9 96.15
QE0012.fits 700 0.75434
78.263 1.2496
8687.5 6296
92.6
QE0024.fits 750 0.8043
69.666 1.2698
6714.2 4158.3 88.9
QE0014.fits 800 0.88938
56.584 1.2911
4473.7 2156
85.17
QE0022.fits 850 0.8485
44.878 1.3225
4939.4 1807.3 81.53
QE0016.fits 900 1.5912
30.209 1.3411
4284.7 1019.1 78.73
QE0020.fits 950 3.9762
14.732 1.4724
11264 1265.6 76.27
QE0018.fits 1000 5.7147
5.0888 1.3814
9821.7 373.16 74.66
QE0036.fits 1100 8.297
0.10033 1.3982
7613.2 5.5222 72.3
The PRISM software provides the quantum efficiency plot as following :
Also a PRNU curve is provided :
For instance, this is some images taken at different wavelength of the same
area of the CCD (bandwidth=5nm and CCD EEV44 backside illuminated ) :

at 320 nm (uniformity degraded by the implantation of P+ passivation layer
annealed by laser after thinning)
at 650 nm (very good uniformity)
at 950 nm (nice fringing !)
Methods used :
The method employed here for QE is straightforward and based on the ratio between
the amount of photon falling to the CCD surface for a given wavelength and the
effective amount of photoelectrons read out at the output of the CCD. This is
achieved by all the data coming from the calibration text files and figures
found in the image file header, such as pixel size, exposure time, flux, wavelength,
etc etc ...
The PRNU computes the histogram of the selected (X1,X2,Y1,Y2) area, and provide
two figures : the intensities at 5% and 95% percentile. Let's call those figures
Int1 and Int2, the PRNU is (Int2-Int1)/(Int1+Int2)*100%

4. Readout noise
The data acquisition process is straightforward : acquire at least five images
in the total darkness having all zero sec exposure.

The input window X1,X2,Y1,Y2 is the window where the noise computation
will take place. Take a window without any kind of defect and showing pure random
noise (avoids hots pixels clusters).
Results :

The above curve is a stacked column mean over all the columns ,and allows
you to display effect that would be drown or hidden by the readout noise .
To trace noise patterns, a Fast Fourier Transform (FFT) of the image is
sometime recommended.
This image shows cosmetic defects (green cross) over a CCD bias image:
these are pixels that are 5 sigma above the median noise + mean.
Console output:
Pixel amount taken to provide median
frame :
noise0005 ->1 42.53%
noise0003 ->2 57.43%
noise0004 ->3 57.65%
noise0002 ->4 42.39%
Noise : 2.286 ± 0.005463 ADU
Pixel amount above 5 sigma : 17100 threshold (ADU) : 6.584
BEWARE : This measurement could be biased
if care has not been taken concerning the file format.
Method used :
The RMS value is computed throughout the selected area. The final noise is the
median noise from the set of the images. To trace bias defect, a median stack
is performed to get rid of cosmic rays, and every pixel which is above or below
five (5) sigmas is referenced as a bad pixel and mapped.
See also this
5. Dark current
As input image data, at least 3 images in total darkness has to be achieved,
having the same exposure time for each (from 5 minutes to 2 hours depending
on the cooling efficiency and CCD temperature).
A mean clean Offset or Bias image MUST to be done as the result of the
median stack of many individual bias frames. Also the conversion factor must
be known accurately.
Be aware that sometimes residual image can disturb dark current measurement,
especially if the CCD is cooled at -120C . Avoid to acquire the data just after
having acquired high level flat fields. To watch this out : take ten dark frames
at the same temperature and check whether or not the mean dark level is decreasing.
Wipe the CCD many times before in the darkness. For instance take 10 darks exposure
of one hour exposure, and do not use the first images (do not select the first
four images).
As usual, the X1, X2, Y1, Y2 window is the window where the computation will
be performed and must be clean of bright defects.
Results
This is the mean of all the columns sent to a single resulting column. The
steps in the curves shows the defect induced by defect columns.. The same is
displayed for the rows.
Here hots pixels map is provided. All pixels above 5 sigma noise+mean are
shown and could be regarded as defects.
Console output:
Loading :F:\Images\Frankie\dark\run1@-120\dark0004.fits
Pixel size information NOT present or NULL in file header, so I take : 15
x 15(µm)
Loading :F:\Images\Frankie\dark\run1@-120\dark0003.fits
Loading :F:\Images\Frankie\dark\run1@-120\dark0002.fits
Loading :F:\Images\Frankie\dark\run1@-120\NoiseMedian.cpa
Integer data type...
Median search :
Compute median frame...
Pixel amount taken to provide median frame :
dark0004.fits ->1 27.92%
dark0003.fits ->2 44.71%
dark0002.fits ->3 27.37%
Offset -> Mean :327.1 Median : 327 ADU
Exposure time (s) = 1800
Dark current : 1.333 ± 0.4714 ADU
Dark current : 5.333 ± 1.886 e-/hour/pixel
Cosmic event rate : 1.195 ± 0.04297 events/min/cm²
Pixel amount above 5 sigmas : 10659 threshold (ADU) : 10.51
Dark current using median frame after median filtering : 5.128 e-/hour/pixel
Even, the software is able to provide the cosmic ray hit rate automatically.
Method used :
The software compute a median stack out of the N provided images and subtract
the bias file to it. The dark current is the remaing amount of adus above the
bias image (positive data). the defects are subtracted automatically as the
difference between individual frames and the median stacked frame.
6. Linearity using TDI method
This method provides the same results as the classical method,
the differences are the following :
- Only one image is necessary (whereas the other method requires many
images and takes long time to be carried out).
- Absolutely insensitive to shutter errors.
- The output curve providing the residual non-linearity versus the
measured signal is continuous (whereas the other method provide
discrete points)
- The measurement accuracy is much better than the one obtained by
the classical different exposure method.
- Not limited by the PRNU of the CCD.
This method has, nevertheless, constraints, where the main drawbacks are
:
- The ability to open the shutter while the CCD readout process has
already began, moreover the shutter must be placed at the entrance of the
integrating sphere, but in any case to share the same focal plane as the
CCD. This, sometimes, can not be achieved with CCD controllers that does
not allow to open the shutter during the readout process. Nevertheless,
manual opening can be used if the CCD is not read out to fast.
The method consists in illuminating the CCD by flat field illumination as
uniform as possible. The intensity of this flat field light (called here Flux=Fl)
must be such as, if T is the CCD readout time and if the CCD is exposed
during a T exposure time yielding to a light intensity of Fl, the resulting
image must be like a flat field of intensity close to 95% the full ADC dynamic.
In clearer words, For instance, if the dynamic is equal to 16bits, the image
must shows up a uniform spatially Flat Field of about 62000 ADUs using the T
exposure time and a flux equal to Fl. Let's assume that the
flux has been set (neutral filter, slit settings) so as to get 62000 ADUs in
20sec exposure time. It means that the CCD MUST be clocked in the way that it
takes about 20 sec to read it out to achieve TDI linearity method.
The image used for the measurement must be acquired using this way : CCD
is started to be readout, shutter being closed, and once the readout of the
first 100 first row has been achieved, the shutter is opened (the shutter
open delay must be neglected compared to the row readout time). The CCD must
be let reading out, being continuously illuminated with a flux equal to Fl.
It is advised to hide also the first 100 rows using a mask (light
shielded), because the readout circuitry might be disturbed (depends on the
CCD) during readout by the continuous light flux to it, and might bias the results.
|
|
Resulting image, display cuts are set to +/-1%
of the Bias level.
|
Same image as the right one, with display cuts
having the full ADC dynamic range from 0 to 65535, the ramp must be
uniform and smooth.
|
So as to reduce this data, the dialog box has to be filled up as following
:
- X1 and X2 horizontal defines the vertical stripe.
- The last and the first row exposed to light (sometimes it's better to
take the 5th row exposed to light)
- The last row which defines the CCD Bias frame level.
- Minimum flux value is meant to threshold the lower range of the intensity
dynamic, to be taken into account for computations and plots.
- Filter : sets how far the output plot curve will be filtered.
- Flat field image is mandatory to correct the data from pixel to pixel
non uniformity, it must be an image taken with the same wavelength and bandwidth
as the TDI image and subtracted from by its bias image.
- Folder : location of the flat field folder (TBC)

Results
Residual non linearity curve, this CCD is linear with +0.43/-0.3
peak-peak and 0.16% rms deviation from the perfect slope.
This curve is a vertical cross section from the selected area,
more exactly the median across this area.
Console output:
Loading :G:\CCDtest\UvesRed\NewLin\eevLeftPort.cpa
Regression slope :17.978; regression Offset :-5956.5
Regression slope :18.028
Regression optimum Offset : -6037
Non linearity (Peak to peak) : 0.43% / -0.2912%
Non linearity (Mean dev.) : -1.875E-13% / rms dev 0.1569%
Method used :
The TDI image is median collapsed towards a single column : a 1D slope is achieved.
The flats field image is used to correct the slope from the fact that all the
pixels of the CCD does not have the same sensitivity. A best linear fit is found
from the slope and non-linearity plot computed. Beware that an infinity of slope
can be found out of a cloud of points, depending on the criteria : less mean
square, weighted points, etc etc...
References :
None : this is a new method developed at ESO.
7. Conversion factor using two bias and two flats
method
This method is very useful for computing the conversion factor during system
development because it is fast and the accuracy is pretty good.
It just needs two biases and two flat field images. It performs conversion factor
measurement using NxM sub windows to avoid any problems due to local defects.
PRISM asks for the amount of windows that is needed across the X and Y axis.
Note that subwindows less than 50x50 pixels can lead to false results, so for
a 1x2K CCD for instance, set 10 windows for the X direction and 20 for the Y
direction. To remove any prescan/overscan area set the X1,Y1,X2,Y2 windows so
as to avoid them. then select the files.

Console output:
Loading :Flat1.fits
Loading :Flat2.fits
Loading :Bias1.fits
Loading :Bias2.fits
For all the windows (540) the results are the following :
window 1=4.49799e-/ADU X1=120
Y1=50 X2=158 Y2=78
window 2=4.11412e-/ADU X1=120 Y1=79 X2=158 Y2=107
window 3=4.31269e-/ADU X1=120 Y1=108 X2=158 Y2=136
window 4=4.14792e-/ADU X1=120 Y1=137 X2=158 Y2=165
window 5=4.0549e-/ADU X1=120 Y1=166 X2=158 Y2=194
..........
window 536=4.45689e-/ADU X1=1836 Y1=253 X2=1874 Y2=281
window 537=4.55087e-/ADU X1=1836 Y1=282 X2=1874 Y2=310
window 538=4.23658e-/ADU X1=1836 Y1=311 X2=1874 Y2=339
window 539=4.01395e-/ADU X1=1836 Y1=340 X2=1874 Y2=368
window 540=4.50764e-/ADU X1=1836 Y1=369 X2=1874 Y2=397
Conversion Factor=4.3775e-/ADU ± 0.012608 for 3457.054ADU
RMS noise =7.0774e- ± 0.092687
Method used :
Note that the algorithm supports flats fields that have different levels of
illuminations, tests have been carried out with flats having means with factor
of 50 between the two images and the feature passed it pretty well ! This method
subtracts the biases from the flat field images, divides the two previous flat
images and computes the RMS value (named N here) and the mean Signal for each
window. Then computes the D=2*S/N^2 figure, from D, the bias noise is removed
and yields to the conversion factor. The corrections due to the different flat
field levels are performed by the software, but not mentioned in this explanation
(to remain clear).
8. Charge transfer efficiency using Fe55 source
This is a very powerful experiment used to derive the vertical and horizontal
CCD charge transfer efficiency (CTE) and also can provide a extremely accurate
measurement of the conversion factor. An Iron (Fe55) radioactive source
is installed 100 mm from the CCD, in the vacuum. This source produces X-rays
(5.9Kev photons) that reaches the CCD surface, creating inside the CCD bulk
1620e- in a 0.5/1um sphere. If those 1620e- are produced within a single
pixel, they should be detected at the output of the CCD readout node as 1620e-
times the conversion factor. Because of "failures" during the charge
transfer, some electrons are lost and remains in the next pixel, and this is
not . This can happen either during the vertical transfer or the horizontal
transfer (serial register). Since the amount of electrons produced by the Fe55
are well defined, it is possible to compute the horizontal and vertical CTE.
A 30 sec exposure image, CCD in front of a Fe55 source

Histogram plot of the whole CCD, pixels from the bias level and the two
peeks of Fe55 (Ka1620e- Kb1778e-)
are visible.
In the dialog form, enter the window to be processed (X1,Y1,X2,Y2). Then
the readout direction (CCD output port direction left/right). The conversion
factor must be known within 5% accuracy. The bias offset level as also to be
provided (accurate, from overscan areas or master bias frame). Select more than
one image is recommended for better accuracy, as so as to enter more than 2
lines for each packet. Those packet are used to bin the histogram of a line/column
N times.

Results
Console output:
Load image: iron-1.cpa
Load image: iron-3.cpa
Load image: iron-2.cpa
Load image: iron-4.cpa
CTEV=1.000000101
CTEH=0.999997222
Conversion factor=0.680809

Horizontal CTE histogram as an image the fact that the slope is left tilted
showed that CTE is lower than 1.0

Vertical CTE histogram as a printable plot (very good V.CTE)

Horizontal CTE histogram as a printable plot (H.CTE =0.999997222 )
Method used :
The software performs vertical histogram gathering N columns so as to have a
better Signal to Noise measurement, it also uses more than one image to improve
the measurement Then displays an image where the X axis is the counts in ADUs,
Y the column number and Z the number of pixels having the given X counts.
The softwarefinds the histogram peaks for every column and fits the best
slope. As you can see on the image above, the slope that joins all the peak
is slightly tilted to the left, showing that the 1620e- created at the end of
the serial register (column 2048) are indeed less than 1620e-, thus showing
a CTE not equal to 1. The software, according to the histogram peak slope can
compute the HCTE.
The same method applies for the horizontal CTE, just swap the word vertical
with horizontal and the word column with rows.
References section
- Electronic imaging in Astronomy, by Ian S.McLean
- Scientific
Charge Coupled Devices, by J.Janesick
- Optical
CCD Detectors - CCD Tests and Characterization at ESO Garching
- Astronomical CCD Observing and Reduction Techniques
Ed. Steve B. Howell
- In
situ CCD testing
This file was updated by C.Cavadore, 17/02/2006